Au cœur de l’intégration de technologies numériques dans les processus de production se trouvent les connexions machines. Elles permettent aux équipements industriels de communiquer et de fonctionner de manière autonome. Ces connexions facilitent l’automatisation, la gestion des données et la coordination en temps réel des opérations de production. Avec l’évolution vers des systèmes intelligents et interconnectés, les connexions machines sont devenues essentielles pour garantir une production efficace, flexible et optimisée.
Les différents types de connexions machines dans l'Industrie
Les connexions filaires
Les connexions filaires sont historiquement les plus utilisées dans les environnements industriels en raison de leur fiabilité et de leur robustesse. Il existe deux types de connexions filaires :
- Ethernet industriel : L’Ethernet est une technologie largement adoptée pour connecter les machines entre elles dans les usines. Il offre un débit élevé, une faible latence et la possibilité de relier plusieurs dispositifs à longue distance. De nombreuses variantes de l’Ethernet, comme l’Ethernet/IP, ont été adaptées aux environnements industriels pour garantir la transmission de données en temps réel.
- Bus de terrain (Fieldbus) : Des protocoles comme PROFIBUS et CAN Bus permettent une communication entre les machines et les dispositifs comme les capteurs et les actionneurs. Ils sont largement utilisés pour la communication locale dans les systèmes de contrôle industriels, en raison de leur stabilité et de leur capacité à fonctionner dans des environnements bruyants.
Les connexions sans fil
Les connexions sans fil gagnent en popularité dans les industries en raison de leur flexibilité.
- Wi-Fi industriel : Dans des environnements où la connexion filaire n’est pas toujours pratique, le Wi-Fi offre une solution flexible pour la communication entre les machines. Cependant, les interférences électromagnétiques et la nécessité de garantir une couverture fiable peuvent limiter son utilisation dans certaines applications critiques.
Bluetooth et Zigbee : Ces technologies sont souvent utilisées pour les capteurs et actionneurs dans les systèmes d’automatisation industrielle. Leur portée courte et leur faible consommation d’énergie en font des solutions idéales pour les dispositifs nécessitant une connexion sans fil à proximité.
Les réseaux industriels spécialisés
Certaines applications industrielles nécessitent des réseaux à faible latence et à hautes performances.
Les réseaux industriels PROFINET, EtherCAT et Ethernet/IP sont spécialement conçus pour garantir une communication déterministe en temps réel, essentielle dans des environnements critiques comme les chaînes de production robotisées ou les systèmes de contrôle de mouvement. Ils assurent des échanges rapides de données entre les machines pour coordonner les actions de manière précise.
La connexion dans le cadre de l’Internet des Objets (IoT)
Les capteurs intelligents et les dispositifs connectés sont désormais intégrés dans les machines pour transmettre des données en temps réel vers des systèmes de gestion centralisés ou des plateformes cloud. Ces connexions IoT permettent une surveillance continue des machines, l’analyse des performances et la gestion proactive des ressources.
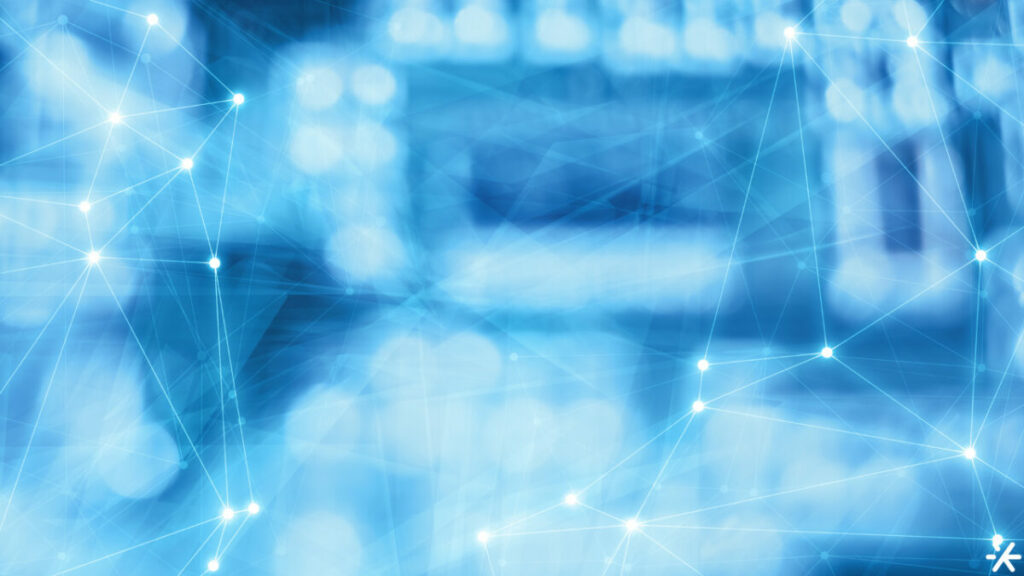
Fonctionnement et avantages des connexions machines
L’automatisation des processus
L’un des principaux avantages des connexions machines est leur capacité à automatiser les processus industriels. En reliant les équipements et les systèmes, ces connexions permettent à chaque machine de recevoir des instructions, de s’ajuster automatiquement en fonction des conditions de production, et de s’auto-corriger pour optimiser le rendement. Cela réduit la dépendance à l’égard des opérateurs humains tout en améliorant la précision et l’efficacité des opérations.
La surveillance et le contrôle à distance
Les connexions machines offrent également des possibilités accrues de surveillance à distance. Grâce aux interfaces centralisées, les opérateurs peuvent surveiller en temps réel l’état des machines et ajuster leurs paramètres à distance. Cela permet non seulement d’optimiser les processus, mais aussi de réagir rapidement aux problèmes potentiels, réduisant ainsi les interruptions de production.
La maintenance prédictive et préventive
En collectant en continu des données sur les performances des machines (comme les vibrations, la température, la pression), les systèmes industriels peuvent détecter des anomalies avant qu’une panne ne se produise. Cela permet de planifier des interventions de maintenance avant que des problèmes ne surgissent, réduisant ainsi les coûts liés aux arrêts de production non planifiés et à la réparation des équipements.
Connexions machines et industrie 4.0
Dans le cadre de l’Industrie 4.0, les connexions machines permettent la mise en place de l’usine intelligente, où les machines, les systèmes de production et même les produits sont interconnectés. Cette interconnexion permet une production plus agile, où les lignes de production peuvent être reconfigurées rapidement pour répondre aux demandes changeantes du marché, tout en optimisant les ressources utilisées.
Voici les avantages clés de la connexion machine dans l’industrie 4.0 :
- La communication en temps réel
La capacité de communication en temps réel est essentielle pour les systèmes industriels qui nécessitent des décisions instantanées, comme les robots ou les systèmes de contrôle de mouvement. La faible latence offerte par des protocoles comme EtherCAT ou PROFINET garantit que les données circulent rapidement, permettant ainsi une coordination précise des actions.
- Exploitation des données avec le Big Data et l’IA
Les machines connectées génèrent d’énormes quantités de données, qui peuvent être exploitées via des technologies de Big Data et d’Intelligence Artificielle (IA). L’analyse de ces données permet non seulement d’optimiser les processus en temps réel, mais aussi d’anticiper les tendances et d’ajuster les opérations pour maximiser la productivité et la qualité.
- Sécurité des connexions industrielles
L’interconnexion accrue des machines soulève cependant des enjeux de cybersécurité. Les systèmes industriels sont de plus en plus exposés aux cyberattaques en raison de leur connexion aux réseaux extérieurs et au cloud. Il est donc essentiel de mettre en place des mesures de protection robustes, comme des pare-feu, des protocoles de chiffrement, et des contrôles d’accès stricts, pour sécuriser ces connexions et protéger les données critiques.
Les connexions machines sont devenues un élément essentiel de l’automatisation industrielle moderne, permettant une production plus rapide, plus précise et plus flexible. Elles jouent un rôle clé dans l’Industrie 4.0, où l’interconnexion des équipements, l’analyse des données en temps réel, et l’automatisation intelligente sont au cœur des stratégies de production.