La démarche TPM, ou Total Productive Maintenance, est une stratégie de maintenance proactive conçue pour maximiser la productivité des équipements industriels en minimisant les pertes et les pannes. Adoptée originellement au Japon, cette méthode s’est répandue à travers le monde en raison de son efficacité dans l’amélioration de la performance globale des installations de production. Cet article vous fournira une compréhension détaillée du TPM, démarche idéale pour toute entreprise industrielle cherchant à optimiser ses opérations.
Qu'est-ce que la démarche TPM?
La démarche TPM, ou « Total Productive Maintenance », est une approche de gestion de la maintenance visant à maximiser l’efficacité des équipements de production. Elle se concentre sur la prévention des pannes et des défauts pour atteindre une production sans défaut, sans accident et sans perte. Originaire du Japon, le TPM a été développé initialement par Nippondenso, une filiale de Toyota, dans les années 1970.
Le TPM est caractérisé par une participation active de tous les employés, des opérateurs aux dirigeants, dans les efforts de maintenance. Il s’agit d’un effort collaboratif pour améliorer continuellement les processus de production. Les principes clés de la démarche TPM incluent :
- L’amélioration continue (Kaizen).
- La maintenance autonome.
- La maintenance planifiée.
- La formation et l’apprentissage.
- La gestion de la qualité.
- La gestion des équipements en début de cycle de vie.
- La sécurité, la santé et l’environnement.
L’objectif final du TPM est d’apporter les différentes valeurs/données afin de calculer un TRS pertinent En appliquant ces principes, les entreprises cherchent à réduire les coûts, augmenter la productivité et améliorer la satisfaction des employés et la qualité des produits.
Les objectifs de la démarche TPM
L’objectif principal de la TPM est de calculer l’indicateur TRS, afin de mesurer le taux d’utilisation d’une installation industrielle pour l’améliorer in fine. Pour y parvenir, la TPM s’attaque aux six grandes pertes : les pannes, les temps de réglage et ajustements, les arrêts mineurs, la vitesse réduite, les défauts de processus, et les défauts de démarrage. En éliminant ces pertes, les entreprises peuvent significativement améliorer leur rendement et réduire les coûts opérationnels.
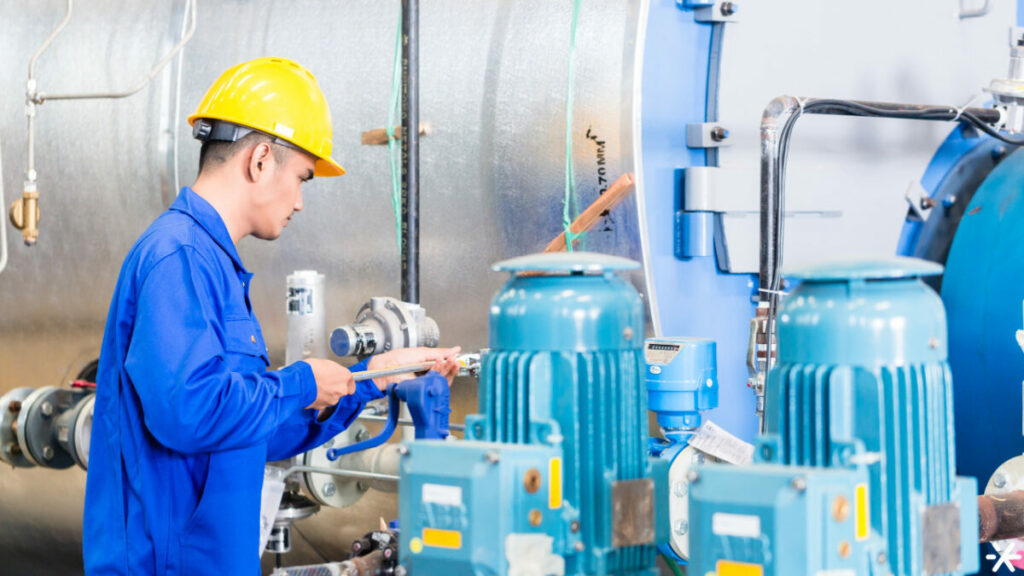
Les Huit Piliers du TPM
- La maintenance autonome
La maintenance autonome est l’un des piliers fondamentaux du TPM. Elle incite les opérateurs à prendre en charge l’entretien courant et les petits dépannages de leurs machines. Cela inclut le nettoyage, la lubrification, et le contrôle de routine. L’objectif est de permettre aux opérateurs de détecter les problèmes tôt et d’anticiper de potentielles pannes, réduisant ainsi les pannes imprévues.
- La maintenance planifiée
Il s’agit de développer des programmes de maintenance préventive basés sur les données historiques des équipements. Cette approche vise à réaliser les interventions de maintenance avant que les défaillances ne surviennent.
- Kaizen : L’amélioration continue
Le Kaizen, ou amélioration continue, est essentiel dans la TPM. Il s’agit d’impliquer chaque employé dans le processus d’amélioration continue des performances des machines et des processus de production.
- La formation et l’éducation et l’apprentissage
Pour que la TPM soit efficace, il est crucial que tous les employés soient formés non seulement à l’utilisation des machines, mais aussi aux techniques de maintenance de base. Cela comprend la formation aux outils de résolution de problèmes et aux méthodes de maintenance préventive.
- La gestion de la qualité
Assurer une production de qualité à chaque étape du processus en détectant et en réduisant les causes des défauts de fabrication.
- TPM dans les services support
Étendre la démarche TPM aux services qui ne sont pas directement liés à la production mais qui influent sur l’efficacité globale, comme le service des achats, l’administration, et les ressources humaines.
- La gestion des équipements en début de cycle de vie
Intégrer les principes de la TPM dès la phase de conception des équipements et des installations pour assurer une maintenance plus facile et plus efficace.
- La sécurité, la santé et l’environnement
Créer un lieu de travail sûr et propre, ce qui réduit les risques d’accidents et augmente la motivation et la satisfaction des employés.
Ainsi, adopter la démarche TPM est plus qu’une simple stratégie de maintenance, c’est un engagement vers l’excellence opérationnelle. En impliquant tous les niveaux de l’organisation, de l’opérateur à la direction, les entreprises peuvent non seulement améliorer leur efficacité mais aussi cultiver un environnement de travail positif et productif. La mise en œuvre de la TPM peut sembler exigeante, mais les bénéfices à long terme pour la compétitivité et la rentabilité sont indéniables.